Does zinc rust? Oxidation and rust eat your metals – and your budget. Protect your metal surfaces and your timelines by using a Cold Galvanizing product.
How Does Zinc Prevent Corrosion?
Read to learn about:
- Preventing Corrosion
- Zinc in Action: Protecting Your Metal Surfaces with Cold Galvanizing
- Accurate Application for Proper Protection
- The ZRC Difference
Preventing Corrosion with Zinc-Rich Compounds
A lesser noble metal will corrode to the more noble. Zinc-rich compounds can be applied by spray or by brush (like a paint) to steel. Zinc, being less noble than steel, forms hydroxycarbonate salt when it corrodes that bonds with the existing zinc in the film coating while upholding galvanic protection. This creates an advanced, self-healing film that ensures the metal surface beneath the coating stays protected.
This works in a 3 step process:
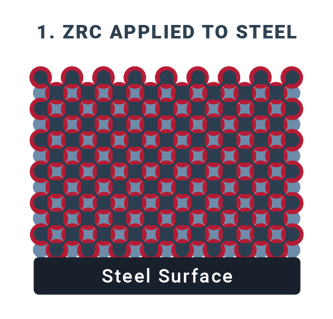
High percent zinc-by-weight in dried film allows electrical current to flow while providing galvanic protection to the steel beneath it. Since zinc is more reactive than steel, it will corrode before the steel does.
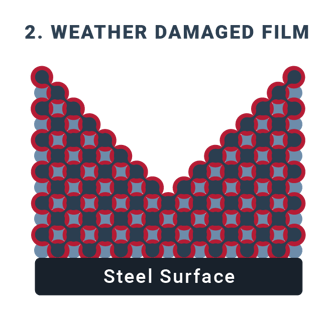
Zinc is a sacrificial anode used to prevent corrosion through cathodic protection. As it corrodes, hydroxycarbonate salt begins to form in the film.
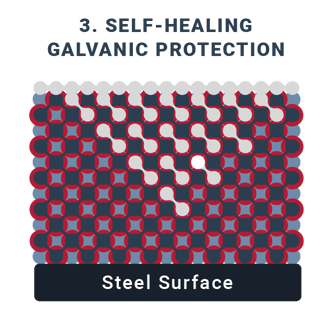
Hydroxycarbonate salt bonds with the existing zinc in the film. This self-healing process creates a dense, impervious, galvanic coating that is resistant to weather, water, and fumes.
Zinc in Action: Protecting Your Metal Surfaces with Cold Galvanizing
Zinc applied as a protective top-coat is a lot easier, and more financially beneficial, to replace than the metal beneath it. A zinc-rich compound has a significantly longer lifespan than that of unprotected, oxidized metal; but it, too, corrodes. Eventually, it will need to be replaced. When that time comes, simply sand or grind the original coating down to remove the zinc hydroxycarbonate salt that has formed. Then, apply a new cold galvanizing compound to keep corrosion at bay.
ZRC is very porous before it sets. Microscopically you'd see that even though the coating has cured, porous pathways exist through the coating. As zinc forms, it fills in those pores, creating a much more dense coating in its final protective state.
If you were to submerge the surface of the metal being coated in water prior to letting the zinc-rich coating cure, the water could seep through down to the metal surface through the capillaries of the porous zinc and create a corrosive threat.
A normal, non-galvanic, paint only acts as a barrier between the corrosion initiating substances and the surface it's protecting. If a barrier paint is scratched or damaged the underlying metal will begin to corrode underneath the paint film, a process known as "undercutting." On the other hand, ZRC coating forms dense hydroxide carbonate salt as it corrodes. When you scratch it down to the bare metal, you cut through that dense salt exposing fresh zinc that begins to corrode and re-bond.
The corrosive reaction is sacrificial; layers of the zinc are sacrificed, or lost, in the reaction that creates the hydroxycarbonate salt. The salt bonds to the zinc while forming.
While the zinc corrodes, the surface it's protecting does not.
You will eventually need to repair or replace the zinc-rich compound protecting your metal surface. The self-healing film provides full protection, buying you time before maintenance or repairs are required.
You will be able to see the scratched surface because the hydroxycarbonate salt heals as a white-colored material.
How long until you'll need to replace your zinc-rich coating?
It all depends on the environment. The other factor would be the surface preparation of the metal prior to applying a zinc-rich coating. Sandblasting the surface will allow you to create a better bond between the zinc coating and the metal, elongating the lifespan of your corrosion protection.
Download the complete guide to Galvanic Corrosion Prevention to learn more.
Proper Protection Depends on Accurate Application
That depends on the condition of the metal. Heavily rusted metal is no longer electrically conductive to the surface. Unless all rust and other impurities are removed from the surface prior to application, the rust will insulate the ZRC coating from the surface and prevent galvanic protection.
For a new metal surface? Surface preparation might be a very simple roughing up of the surface followed by a solvent bath to remove the dust and dirt.
Learn more about types of ZRC applications in this blog post.
The ZRC Difference: Unmatched Corrosion Protection
There are many products that service the varying needs of the corrosion prevention industry. Imitation is flattering, but the proof is in the paint. ZRC Worldwide created zinc coating technology as a hot-dip alternative to combat corrosion and has been a worldwide leader in the space for almost 70 years.
Whether touching up an existing project or completing a full-sized job from scratch, our team will ensure you get the right product and the correct application method for your needs.